Need for Quality Journey & Quality Methodologies: Talk by Arun Kaushik, Amazon
In the previous article, we saw the definition of quality and the difference in the perception of quality. Let's look at how quality has evolved over the years and the need for quality.
Evolution of the Meaning of Quality over Time
The basics of quality are ISO, Conformance, SOPs, Documentations, et cetera. Then organisations moved into some of the low complexity initiatives. Organisations primarily in the manufacturing sectors are more into Kaizen and Quality Circles.
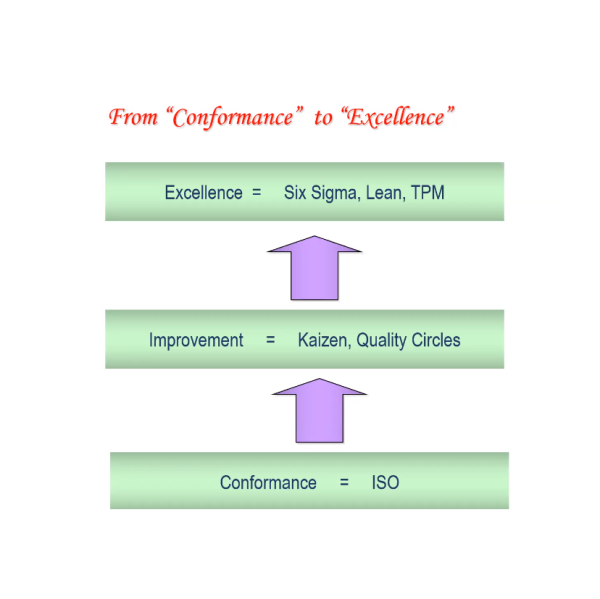
From 'Conformance' to 'Excellence'. Source Credit Arun Kaushik
Then organisations started adopting Excellence initiatives like Six Sigma, Lean, TPM. Although this journey is still very prevalent, the latest is about AI, Machine Learning etc. But the basic tenets of all those methodologies related to these underlying concepts such as Six Sigma, Lean, Kaizen remain the same. These are the fundamental pillars of any organisation which is adopting a quality culture.
Any organisation which aspires to grow to the next level should have quality at the heart of it. The basics have to be quite robust and strengthened appropriately. Why? Because these have been the lever for all the organisations which have grown significantly. Whatever we do today, the goal should be to do it more efficiently with speed.
How Do Organisations Relate to Quality Methodologies?
There are different ways in which various organisations have adopted these methodologies. Some organisations have called these initiatives business excellence. Some have called it operational excellence, and others call it quality assurance. Some organisations call them Kaizens, Quality Circles, Process Excellence, Lean Six Sigma. Therefore, different organisations have attributed different names to the quality culture they are pursuing.
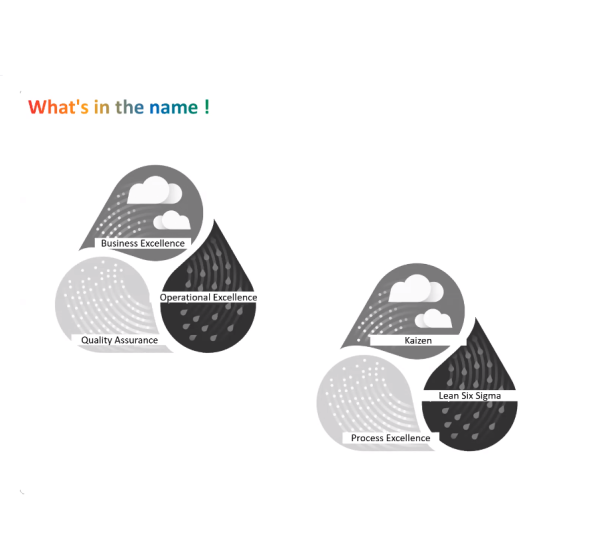
Nuances in a name! Source Credit: Arun Kaushik
The basic underlying theme remains the same: It is all about working towards improvement. The name given has nuances in terms of the results that we envisage for the organisation's performance. For different model frameworks, expectations from each are different. If one calls it Business Excellence, that is a different model. If another organisation calls it Operational Excellence, then, of course, the objectives vary. But at the same time, the name given is significant for any organisation adopting these methodologies. And the way they drive them is also different.
How are you driving the improvement culture? Are you doing it bottom-up or top-down? Is it through Kaizens and the Quality Circles? That again is a framework that organisations adopt, looking at the different expectations from the quality culture.
Need for Quality Culture
For any organisation, quality is a support function. It is also a cost function but with different expectations. For instance, one does not put up a machine in a manufacturing sector expecting that the device will transform into something meaningful for the customer. Similarly, if you look at the quality support function, there is cost while putting up the resources and infrastructure. There are some real expectations aligned to this cost. These functions are also supposed to deliver something, and those expectations have to be crystal clear.
The quality standard and methodology decisions have to be taken right away for the organisation by the management. It is imperative to deliver the expected outcome rather than have an aesthetic function not aligned to the entire organisation and does not become the centre of all the action.
In successful organisations, every function has someone or the other working in the excellence initiative. So it is that important: Everyone works on quality, every hour of the day.
Quality as a Function of the Organizational Goal
How do we address the entire architecture of the quality function? How do we keep it at the forefront of all the initiatives? The only objective of this function is improvement. We should link those improvement initiatives to the organisation's overall goals.
There are various quality functions an organisation is supposed to do. There should be unambiguous guidelines to choose the right path at the right time on a quality journey. It is not about having some of the processes streamlined, some ISO certification, but it should be very clearly related to the organisational goal.
While the objective is quality and its improvement, two broad goals are maximising the revenue flowing in and minimising costs. With these objectives in mind, how do you stage your quality function? Whatever quality work we undertake has to help the organisation either gain revenue or reduce cost. The processes thus chosen should justify the entire architecture of our focus on quality.
The personnel chosen is a significant pillar of quality capability. Companies need the right trained people for adopting this. They have to be as diverse as possible to bring in new ideas. Collaborations should be there in place across functions, across different silos. Each functional piece might work differently; for instance: Marketing might work in one way, while the supply chain might work in an entirely different way. Both might be doing excellently on their functional priorities. But the organisation as a whole might be losing out in terms of the overall deliverables. So collaboration is essential, and so is a common purpose.
It is also essential to keep a close watch on industry trends to leverage digital investments. It would be best if you were looking at the trends and competition. The adoption of quality culture in the organisation has to sync with how the industry is moving.
The process part of it across any organisation needs to be in place irrespective of the change in people because people will keep changing. There is a need for a robust process system where the standards are defined, and references are built-in for the various risk contingencies and essential operational procedures. These are some of the foundational pieces in terms of having the basics in place. So that stays anchored.
Similarly, another big lever is the monetisation of the assets. Ola and Uber are some of the companies that are leveraging asset monetisation by utilising the ideal asset. In the example, later on, you will see how assets can be well monetised, inventory turnover monitored, waste removal optimised, turnaround time improved, Service Level Agreements (SLAs), response time reduced, et cetera.
Large organisations that are the market leaders have one of the fastest processes in terms of the response time, in terms of how they are structured to respond to the customer needs. These are some of the insights about the critical enablers while we are driving the quality culture.
(Talk by Arun Kaushik Paraphrased by Nisha Oommen)